What is Porosity in Welding: Key Elements and Their Effect On Weld High Quality
What is Porosity in Welding: Key Elements and Their Effect On Weld High Quality
Blog Article
The Scientific Research Behind Porosity: A Comprehensive Overview for Welders and Fabricators
Comprehending the complex mechanisms behind porosity in welding is vital for welders and makers pursuing impressive craftsmanship. As metalworkers explore the depths of this phenomenon, they uncover a world governed by various elements that affect the formation of these minuscule voids within welds. From the composition of the base materials to the details of the welding process itself, a wide variety of variables conspire to either worsen or reduce the visibility of porosity. In this comprehensive guide, we will certainly unwind the science behind porosity, exploring its effects on weld quality and introduction progressed methods for its control. Join us on this journey through the microcosm of welding flaws, where accuracy meets understanding in the search of remarkable welds.
Comprehending Porosity in Welding
FIRST SENTENCE:
Assessment of porosity in welding reveals vital understandings into the honesty and quality of the weld joint. Porosity, identified by the presence of cavities or spaces within the weld metal, is a typical problem in welding processes. These spaces, otherwise correctly addressed, can jeopardize the architectural honesty and mechanical residential properties of the weld, leading to prospective failings in the ended up product.
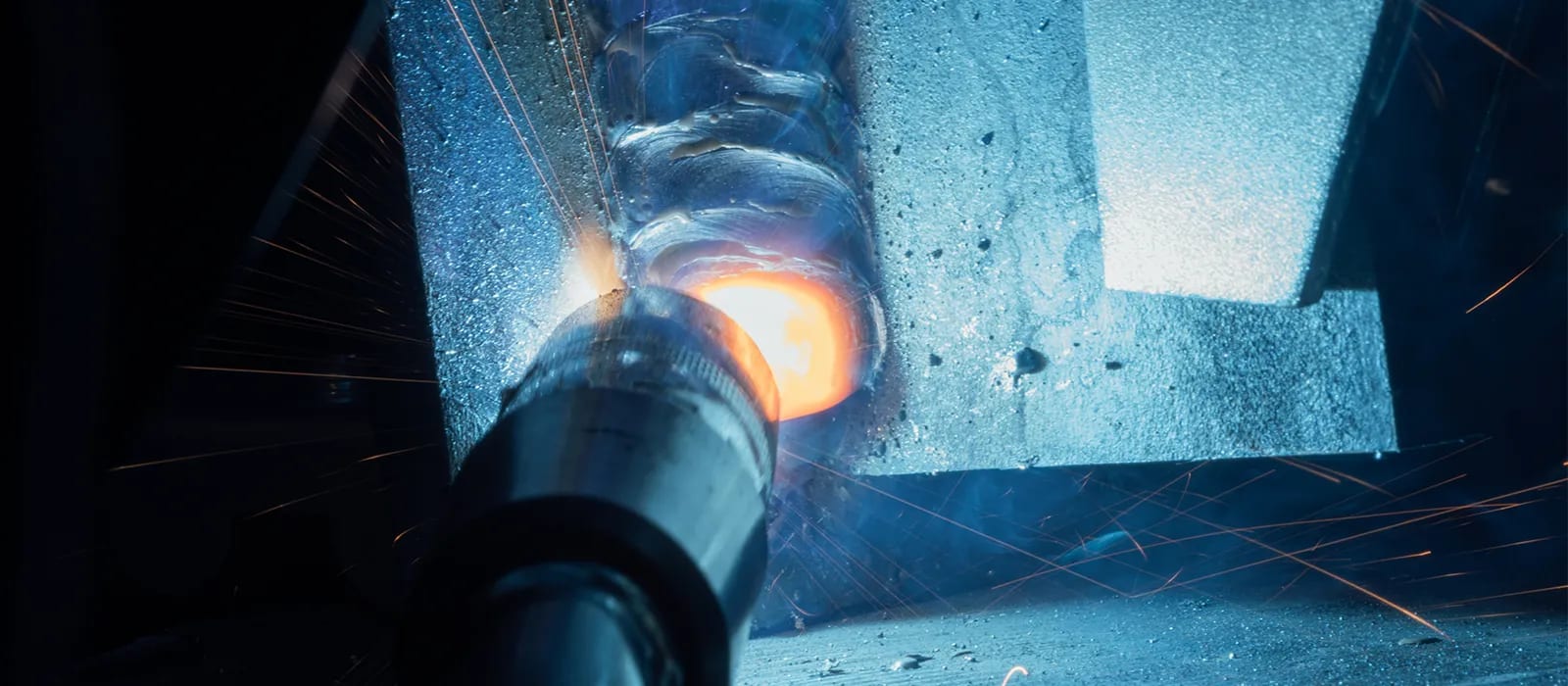
To identify and evaluate porosity, non-destructive testing techniques such as ultrasonic testing or X-ray inspection are often used. These strategies enable the recognition of inner issues without endangering the integrity of the weld. By examining the dimension, form, and circulation of porosity within a weld, welders can make informed choices to boost their welding processes and achieve sounder weld joints.
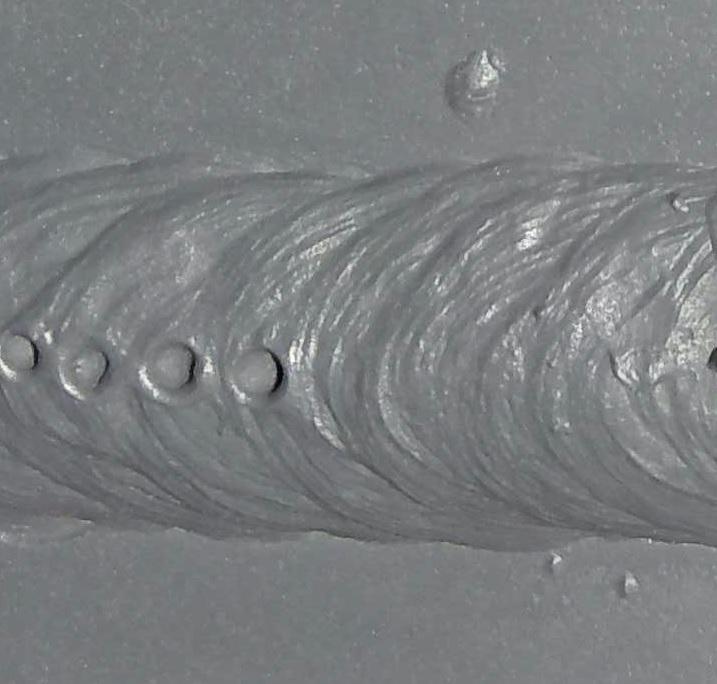
Elements Affecting Porosity Formation
The event of porosity in welding is influenced by a myriad of elements, ranging from gas protecting performance to the details of welding specification setups. Welding parameters, including voltage, existing, travel rate, and electrode kind, additionally impact porosity formation. The welding strategy employed, such as gas metal arc welding (GMAW) or secured metal arc welding (SMAW), can affect porosity formation due to variations in heat distribution and gas protection - What this website is Porosity.
Results of Porosity on Weld Top Quality
Porosity formation dramatically compromises the structural integrity and mechanical buildings of welded joints. When porosity is existing in a weld, it develops spaces or dental caries within the product, decreasing the overall stamina of the joint. These gaps function as stress concentration points, making the weld a lot more at risk to cracking and failing under load. The visibility of porosity also compromises the weld's resistance to deterioration, as the caught air or gases within deep spaces can react with the surrounding environment, resulting in degradation gradually. In addition, porosity can hinder the weld's ability to try this site endure stress or influence, further threatening the total quality and reliability of the welded structure. In essential applications such have a peek at this site as aerospace, automotive, or structural building and constructions, where safety and toughness are critical, the destructive effects of porosity on weld top quality can have severe effects, stressing the significance of lessening porosity via correct welding strategies and procedures.
Techniques to Decrease Porosity
To boost the quality of bonded joints and make sure architectural integrity, welders and producers employ particular techniques targeted at reducing the development of voids and cavities within the material during the welding procedure. One efficient technique to decrease porosity is to guarantee proper material preparation. This includes complete cleaning of the base steel to remove any type of contaminants such as oil, oil, or wetness that can add to porosity formation. Furthermore, utilizing the appropriate welding criteria, such as the proper voltage, existing, and take a trip speed, is crucial in preventing porosity. Keeping a constant arc size and angle during welding additionally assists reduce the possibility of porosity.

Furthermore, choosing the ideal protecting gas and maintaining proper gas circulation rates are important in lessening porosity. Making use of the suitable welding technique, such as back-stepping or using a weaving activity, can additionally help disperse heat equally and minimize the possibilities of porosity development. Making sure proper ventilation in the welding setting to remove any potential sources of contamination is essential for attaining porosity-free welds. By carrying out these techniques, welders can effectively reduce porosity and produce top quality bonded joints.

Advanced Solutions for Porosity Control
Applying innovative technologies and cutting-edge techniques plays a critical role in attaining remarkable control over porosity in welding procedures. In addition, employing innovative welding techniques such as pulsed MIG welding or customized environment welding can likewise assist alleviate porosity problems.
Another advanced solution entails the usage of sophisticated welding tools. Using tools with integrated attributes like waveform control and sophisticated power sources can boost weld quality and decrease porosity dangers. In addition, the application of automated welding systems with exact control over specifications can substantially reduce porosity flaws.
Furthermore, incorporating advanced monitoring and inspection technologies such as real-time X-ray imaging or automated ultrasonic testing can help in identifying porosity early in the welding process, permitting instant rehabilitative activities. Generally, integrating these advanced solutions can substantially improve porosity control and boost the overall top quality of bonded elements.
Conclusion
In verdict, comprehending the science behind porosity in welding is necessary for welders and fabricators to generate high-quality welds - What is Porosity. Advanced options for porosity control can further improve the welding procedure and ensure a strong and trustworthy weld.
Report this page